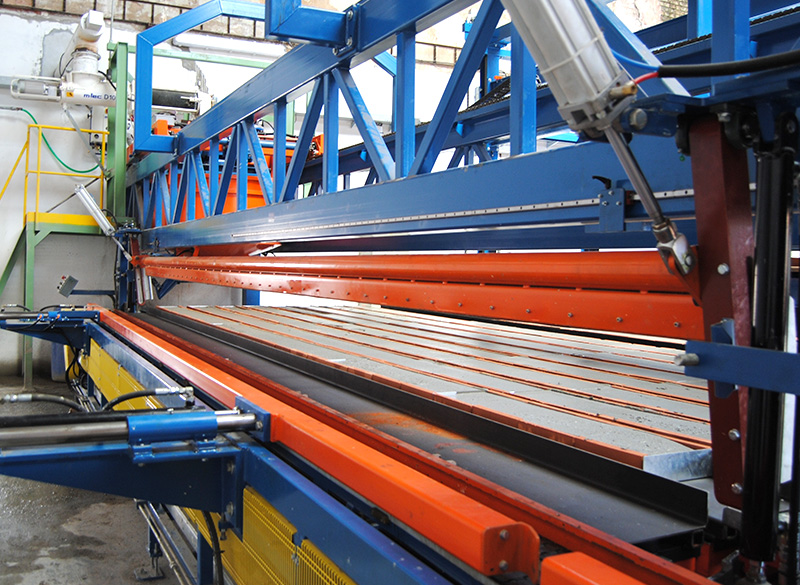
Brick-cement beams and lintels system
Born from the SIMEM SPIL expertise in automated carrousels, BRICKBEAM is a brick-cement beams and lintels system and brick-cement lattice girder beams.
Legenda
- Brick feeder with jib crane for manual loading
- Feeding line of bases and reinforcement
- Initial head including elevator for empty trays
- Casting and vibrofinishing station
- Tower curing magazine
- Demoulding station
- Final head with automatic station for recovering
the cleaned trays - Unloading line with jib crane for manual stacking
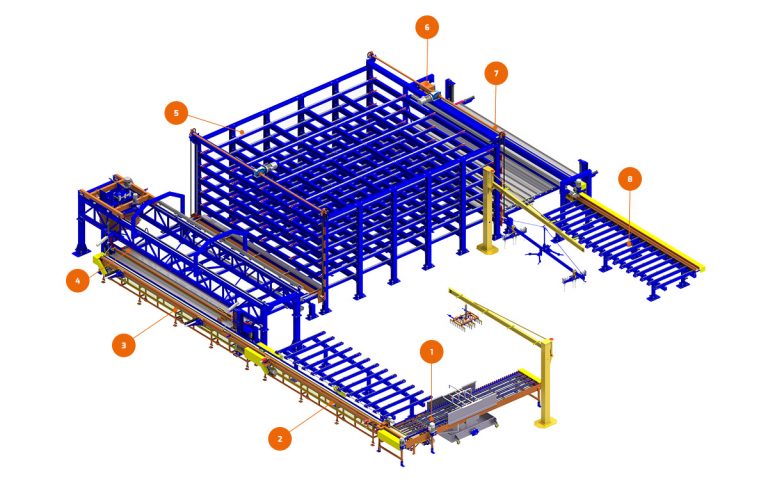
The process
1. Brick feeder with jib crane for manual loading. The operator loads an entire level of bases, as taken from the pack. The feeder includes the wetting pump and the device to turn the bases upside down.
5. Tower curing magazine with 7 levels, including the elevator with automatic pusher that loads the trays in the tower and the lowerator with automatic extractor, that picks the trays after curing
2. Feeding line of bases and reinforcement. It includes the framework station, with suitable front loader for bars and lattice, consisting of 16 motorised chains.
6. Demoulding station includes the mobile self-propelled carriage on its own gantry single track, with extractor designed to extract from the head the row of items, one tray at a time. It includes motorised brusher and the device to distribute the release oil on cleaned trays.
3. Initial head including elevator for empty trays, which automatically lifts the tray to the operative level, and the pusher with 8.5 m long bar which automatically moves over sideways and loads on the tray the dry reinforced bases
7. Final head with automatic station for recovering the cleaned trays, it includes the lowerator that lowers one tray at a time to the lower level, where the tray is taken back to the initial head.
4. Casting and vibrofinishing station includes the self-propelled automatic batching carriage, mobile on its own gantry tracks, and the vibro-compacting devices. To manage various shapes of bases, a suitable pneumatic device automatically descends and moves against the free side of the bases, automatically adapting to the real width of the bases, to assure stability and alignment of the items, during vibro-compacting.
8. Unloading line with jib crane for manual stacking. The items extracted by the extractor are automatically moved into the motorised belt that takes them and aligns them for unloading. Unloading is performed sideways by an 850 cm long bar, which transfers the row of items from the motorised belt to the unloading table. The unloading table consists of a motorised set of 16 parallel belts, with stainless steel slats, that guide and collect forward the lines of items. At the end of the belts, using the jib crane by using suitable interchangeable forks (based on the type of item) the operator picks the finished product and stacks it, ready for transport to destination.